Parasoleil’s unique line of laser-cut patterned panels may look easy to make, but they are embedded with years of manufacturing expertise, powdercoat finishing practice, design trial and error, and engineering sweat that evokes the thought, “it just looks so easy.” Do not be fooled – just because it looks easy, does not mean it is. The Cortivale Package is the sum of all that hard work that goes into every panel that Parasoleil makes.
When approaching a new commercial architectural project, multi-family residence, or a public park, it requires a complete understanding of how manufacturing and engineering impacts a pattern and its design. The project may rely on structural calculations to adhere to International Building Code — a small but significant component of the process allowing each jurisdiction to determine if a project can be permitted to proceed. The entire process includes how a panel is made, knowing what design options an architect has while staying within budget, and knowing which manufacturer has the experience and expertise to understand the complexities of a seemingly simple, decorative product.
This package is a three-part approach to structural and design integrity for our system of versatile laser-cut metal panels, engineered patterns, and patented hardware. This comprehensive approach to product integrity is built into every project, whether it’s a bolt-together product, a pre-engineered pattern that can be customized to fit a unique space, or a fully custom approach that still needs to fit the budget.
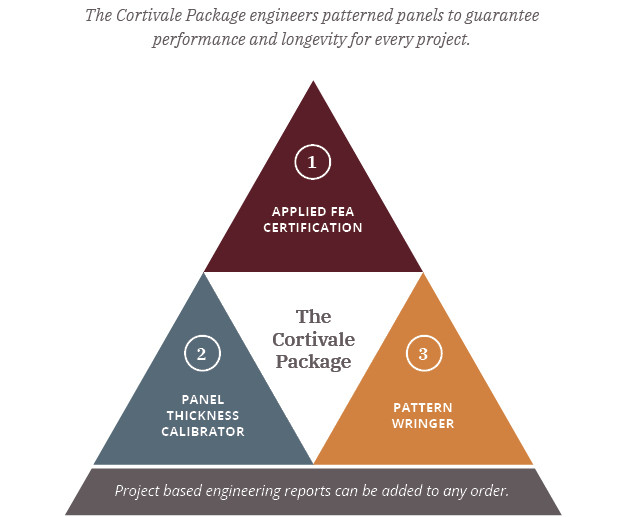
1. Applied FEA Certification: Our customizable system of panels, hardware, and structural support has been tested and certified by IAPMO (International Association of Plumbing and Mechanical Officials EGS) for high allowable pressures to guarantee our product meets Finite Element Analysis and specific building requirements better than any substitute. Building Code provides conservative guidelines that can be applied to many different types of structures, site conditions, uses, and building materials. This is what project engineers use when nothing else is available. There are 3 ways to comply with IBC guidelines ignore engineering and hope that the structure passes permitting (we don’t recommend this), test the custom assembly for each site condition to make sure it doesn’t fail (not an inexpensive or short process), or have the product tested, but then authenticate its structural integrity with certification that can be applied to a variety of customizations and site conditions. The Cortivale Package is built on the last option. Parasoleil gives clients the peace of mind that we have already thought through and mitigated the risks associated with custom fabrication for commercial buildings. If not carefully considered, it can be difficult to stay on-time, on-spec, and on-budget.
2. Panel Thickness Calibrator: The PTC is a tool developed by Parasoleil that will quickly determine the optimal panel thickness for your project based on a database of thousands of product combinations and hundreds of nuanced site conditions. This tool allows for an easy mix-and-match design experience that instantly tells you which patterns, brackets, structural spans, and panel thicknesses will work best for your budget and performance requirements. Too thick and you are wasting money. Too thin and you may have a structural integrity issue. The PTC helps you find the perfect balance.
3. Pattern Wringer: Translating 2-D pattern drawings to laser-cut metal panels presents a host of challenges that can be exceedingly difficult to anticipate. The Pattern Wringer is a process whereby our engineers and designers apply their vast expertise and knowledge to any design and work out any potential issues before they are realized in production. This technical evaluation of a pattern ensures there will be no heat warping during the manufacturing process which is critical for ensuring material structural performance. While aluminum is lightweight, never rusts, and needs less structural support than steel, its molecular composition can change with concentrated heat, causing the performance of the panel to differ from FEA results and wet stamp . This could result in the liability being passed on to the project engineer who stamped it, or the panel is over-engineered to allow for some warping during manufacturing producing a thicker, more expensive panel or labor in structural support. Parasoleil has developed another approach where engineering expertise and manufacturing feasibility is built into our design process with the Pattern Wringer.
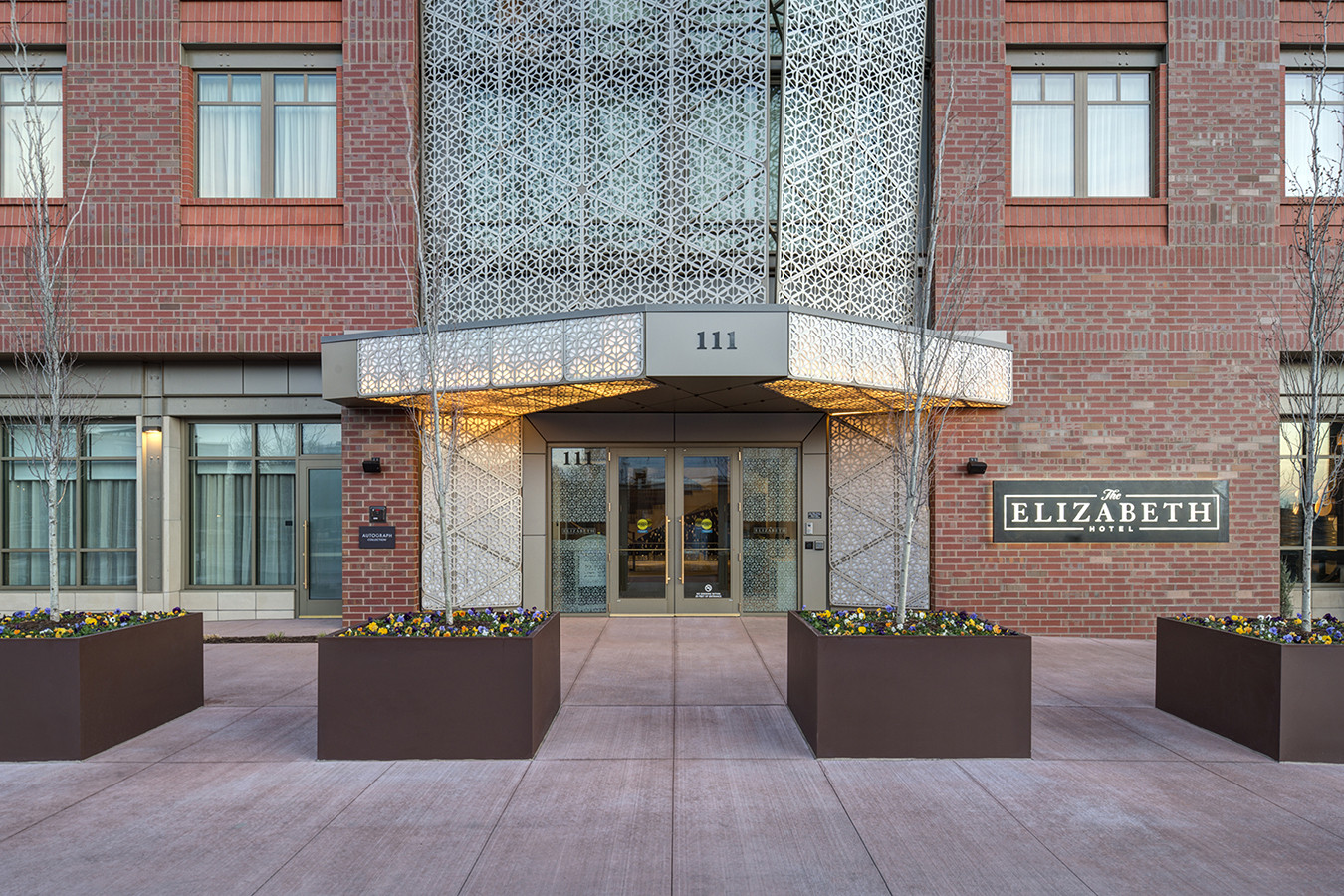
As a complete package, Cortivale ensures we consider every aspect of design, engineering, manufacturing, and performance of the product with every project that we take on. Through this package, Parasoleil has been able to provide maximum value to our projects and customers. With a focus on design integrity and structural assurance, we strive to bridge art and the environment, creating long-lasting places where people want to be.
More on the Cortivale Package here or reach out to our team to get started on your project.